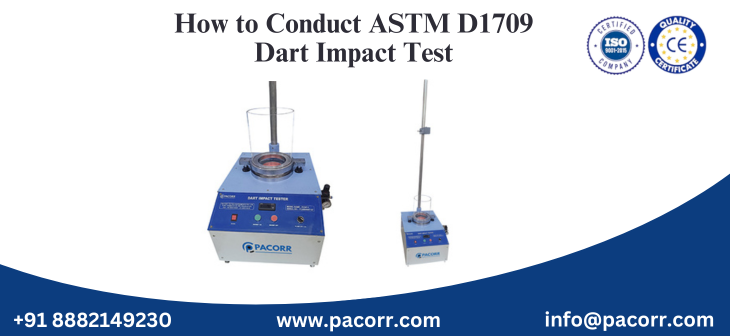
Pacorr provides advanced quality testing solutions for packaging materials, and one of the most vital instruments in their lineup is the Dart Impact Tester. This equipment plays a critical role in determining the impact resistance of plastic films and sheets, which is essential for maintaining product integrity during handling and shipping. To ensure accurate and reliable results, both calibration and proper operation of the dart impact tester are crucial. In this comprehensive guide, we’ll walk you through every step of the calibration and operational process, along with valuable tips to help you optimize testing efficiency.
This guide also highlights essential keywords like dart impact tester, dart impact tester price, and dart impact tester manufacturer to support users in selecting the right solution and ensuring compliance with testing standards.
Understanding the Dart Impact Tester
A dart impact tester is a specialized instrument used to measure the energy required to cause a failure in plastic films by the free-falling dart method. This test helps determine the material’s toughness and its ability to withstand sudden impacts during packaging, transport, and use. It is particularly important in industries such as FMCG, agriculture, pharmaceuticals, and industrial packaging.
Why Calibration and Proper Operation Matter
Accurate calibration and standardized operation procedures are essential to:
- Eliminate human error
- Ensure repeatability of results
- Comply with ASTM D1709 and other testing standards
- Maintain reliability in R&D and quality control environments
- Support production decision-making processes
Step-by-Step Dart Impact Tester Calibration Guide
Before initiating any testing, it’s vital to calibrate the dart impact tester to ensure its measurements are precise. Here’s a structured calibration process:
1. Verify Dart Weights and Assembly
- Check if all dart weights are available and match the specified increments (commonly 5 g).
- Confirm that the dart head conforms to standard dimensions (Type A or Type B as per test method).
- Ensure dart shaft is clean, undamaged, and properly secured to the weights.
2. Calibrate Drop Height Mechanism
- The standard height for Type A dart is 660 mm and for Type B is 1524 mm.
- Use a calibrated height scale or laser measurement tool to verify the exact drop distance from the release mechanism to the impact surface.
- Make adjustments to the frame or clamps to ensure height accuracy.
3. Check the Electromagnetic Release System
- Test the electromagnetic release for smooth operation.
- It should release the dart instantly upon triggering, with no delay or resistance.
- Replace or repair if the magnet exhibits inconsistent behavior.
4. Level the Base Plate
- Place a precision level gauge on the base where the specimen is fixed.
- Adjust screws or base feet to ensure it is perfectly level. This helps prevent dart tilt or misalignment.
5. Run a Control Test with Known Material
- Use a reference sample with known impact strength.
- Drop the dart from the calibrated height and record the energy required to cause failure.
- Compare results with expected values to validate the setup.
- If discrepancies occur, re-check height, weight, and sensor calibration.
Standard Operation Procedure for Dart Impact Tester
After calibration, the next step is to operate the machine correctly to obtain valid data. Follow these steps to achieve optimal results:
1. Sample Preparation
- Cut plastic film samples into standard sizes (usually 240 mm x 240 mm).
- Ensure samples are clean, wrinkle-free, and conditioned at standard atmospheric conditions (usually 23°C and 50% RH for 24 hours before testing).
2. Mounting the Sample
- Secure the sample tightly across the circular clamp or holder without stretching it beyond its natural tension.
- Make sure no air bubbles or folds are present.
3. Select Dart and Weight Combination
- Start with a dart assembly at a mid-range weight.
- Add or remove weights based on preliminary test runs.
4. Set Drop Height
- Lock the dart at the required height according to the method (Type A or B).
- Ensure the height is aligned and the release mechanism is reset properly.
5. Conduct the Test
- Press the release button or trigger to drop the dart.
- Observe whether the sample ruptures upon impact.
- Record the result (pass or fail) and note the weight and drop height used.
6. Follow the Staircase or Bruceton Method
- After each test, adjust the weight upward or downward depending on the result.
- Continue until you determine the 50% failure point.
- Calculate the mean failure energy using statistical formulas defined in ASTM D1709.
7. Document and Analyze Results
- Record all readings in a test log.
- Plot results if required for presentation or further analysis.
- Use data to improve film formulation or assess quality consistency.
Safety Precautions During Operation
Operating a dart impact tester involves high-speed components and falling weights. Always observe the following precautions:
- Keep hands away from the dart path and clamps during release.
- Ensure that all operators are trained in safety protocols.
- Regularly inspect the device for loose parts, wear, or electrical issues.
- Use protective barriers or guards if testing in a high-traffic lab environment.
Maintenance Tips for Long-Term Accuracy
- Clean the dart head and shaft after every 10 tests to remove debris or static charge.
- Recalibrate the machine monthly or after every 100 tests.
- Store dart weights in a moisture-free container to avoid corrosion.
- Replace worn-out clamps or rubber pads as needed.
- Keep a logbook of calibration and maintenance schedules.
Choosing the Right Dart Impact Tester Manufacturer
When investing in a dart impact tester, it is important to choose a reliable manufacturer who ensures accuracy, consistency, and long-term support.
Here’s what to look for in a trusted dart impact tester manufacturer:
- ISO-certified production facility
- Compliance with ASTM D1709 or ISO 7765-1
- Availability of digital display for impact energy
- Modular and easy-to-maintain design
- Competitive dart impact tester price for the features offered
- Prompt technical support and calibration assistance
Pacorr is known for delivering industry-leading equipment that meets all these criteria, making it a preferred choice among R&D labs and packaging manufacturers.
Final Thoughts
Pacorr's dart impact tester is engineered to deliver precise, repeatable, and standard-compliant testing of plastic film materials. By following a structured approach to calibration and operation, manufacturers can ensure their packaging materials withstand real-world handling conditions. Whether you're concerned about dart impact tester price, reliability, or support, investing in a high-quality machine from a reputable dart impact tester manufacturer ensures your quality control process is never compromised.
Thanks to Pacorr Testing instruments, we have all the required quality testing instruments that have helped us to ensure the best quality delivered to our clients.
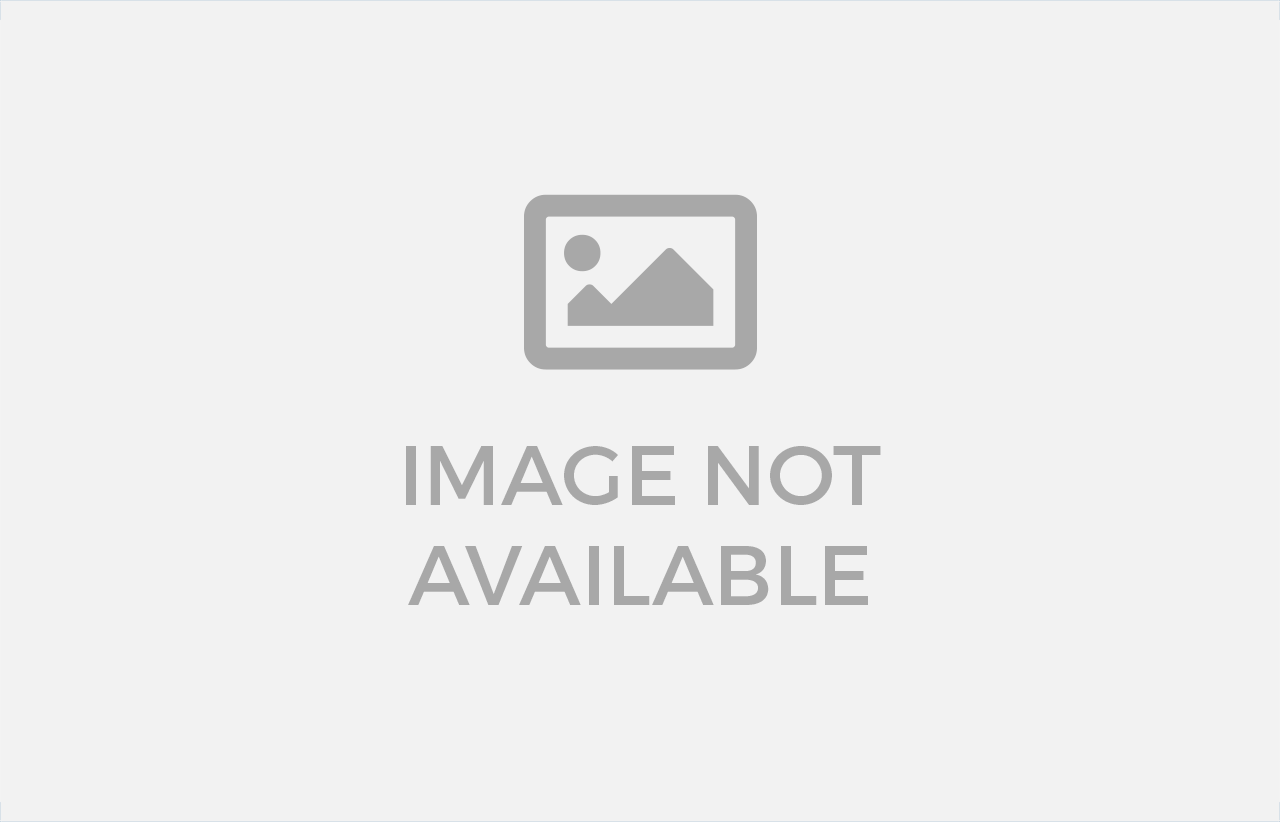
Danish
Fair Exports Pvt. Ltd.