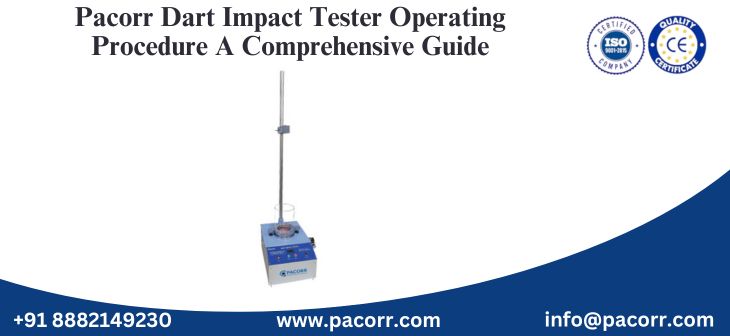
Pacorr is a trusted name in the field of material testing instruments, known for delivering precision-engineered tools that meet the demanding quality standards of modern industries. Among its most relied-upon instruments is the Dart Impact Tester—a robust solution used primarily to evaluate the impact resistance of plastic films, packaging materials, and related substrates. This guide provides a step-by-step breakdown of the Dart Impact Tester operating procedure, offering valuable insights for quality assurance professionals, production engineers, and anyone involved in packaging R&D.
As a leading dart impact tester manufacturer, Pacorr brings decades of practical experience and engineering know-how to ensure reliability and accuracy in every test. Whether you are working in pharmaceuticals, FMCG, food and beverages, or industrial packaging, understanding how to correctly operate a dart impact tester is crucial for maintaining consistent product performance and reducing the risk of failure in real-world conditions.
What is a Dart Impact Tester?
A Dart Impact Tester is a laboratory device used to measure the impact strength of flexible films, typically plastic sheets or laminates. The purpose of this test is to simulate real-world stresses that materials may encounter during handling, shipping, or usage. The instrument evaluates the weight of a free-falling dart required to cause failure in the sample, providing a quantitative value for impact resistance.
There are primarily two testing methods: Method A (using a hemispherical dart) and Method B (using a different dart geometry and impact height). Both are standardized under ASTM D1709, a widely accepted testing protocol for plastic films.
Why Dart Impact Testing is Important
The packaging industry has evolved rapidly in the last decade. With increasing demands for durability, sustainability, and consumer satisfaction, manufacturers must ensure that their packaging can withstand mechanical stresses without rupturing or degrading. Dart impact testing plays a key role in this quality control process by:
- Predicting performance in real-life logistics
- Minimizing material waste due to over-engineering
- Ensuring compliance with international standards
- Reducing the risk of product returns and damage
Manufacturers and QA teams rely on accurate test data to refine material formulations and optimize thickness without compromising on strength.
Key Features of Pacorr’s Dart Impact Tester
As a reputed dart impact tester manufacturer, Pacorr integrates several user-focused features to enhance precision and ease of use:
- Digital and manual models available based on testing requirements
- Pneumatic clamping for uniform specimen placement
- Adjustable drop height with safety lock features
- High-precision dart heads made from corrosion-resistant material
- Digital display for impact energy and pass/fail results
- ASTM D1709 compliance
These features allow for controlled, repeatable, and traceable testing conditions, which are vital for maintaining quality standards in regulated industries.
Step-by-Step Operating Procedure
Operating the Dart Impact Tester involves a combination of mechanical setup, sample preparation, and execution. Below is a detailed step-by-step guide:
Step 1: Preparing the Sample
Begin by cutting the sample material according to standard dimensions—usually around 150mm x 150mm. Ensure that the film is clean, free from wrinkles, and does not have any pre-existing defects that could skew results.
Step 2: Securing the Sample
Place the sample over the clamping area of the tester. Use the pneumatic or manual clamp (based on your model) to hold the sample tightly. An unevenly clamped sample can produce inaccurate or inconsistent results.
Step 3: Selecting the Dart
Choose the appropriate dart based on the type of material being tested and the testing method (A or B). The dart’s weight can vary, so make sure to start with a mid-range value if you’re unsure and adjust based on test outcomes.
Step 4: Setting the Drop Height
Adjust the drop height of the dart according to the standard being followed (usually between 660mm and 1524mm). This step is critical since drop height directly affects the impact energy delivered to the sample.
Step 5: Performing the Test
Raise the dart to the selected height using the guide mechanism. Release the dart, allowing it to free-fall onto the center of the clamped sample. The system may automatically detect whether the sample has failed (penetration or rupture).
Step 6: Recording and Analyzing Results
Note whether the sample passed or failed. Repeat the process across multiple samples to determine the minimum dart weight required to cause failure in 50% of the test specimens—this is referred to as the mean failure point. Statistical methods like the staircase method or Bruceton analysis may be used for higher accuracy.
Safety Precautions to Follow
While Dart Impact Tester are relatively safe to operate, there are several safety protocols that must be adhered to:
- Always wear protective gear, especially safety goggles
- Ensure the area around the tester is clear of personnel during testing
- Never attempt to adjust the sample or machine when the dart is elevated
- Use guards and interlocks provided by the manufacturer to avoid accidents
Common Mistakes and How to Avoid Them
Even experienced users can occasionally make errors during testing. Here are a few pitfalls to watch out for:
- Incorrect sample placement: Misaligned samples lead to edge hits instead of center impacts.
- Wrong dart weight: Starting with too high a weight can damage the machine or sample.
- Ignoring temperature/humidity: Environmental conditions can influence film strength and should be controlled.
Following best practices and standardizing your operating procedure helps maintain result consistency across batches and operators.
Maintenance Tips for Longevity
Like any precision equipment, Dart Impact Testers require regular care. Here are some essential maintenance pointers:
- Clean the clamp and drop tube regularly to avoid residue build-up
- Check the calibration of the drop height and dart weight periodically
- Lubricate moving parts as recommended in the user manual
- Inspect the dart heads for wear or deformation
Keeping your tester in top condition not only ensures accurate readings but also extends the lifespan of the device.
Industries That Rely on Dart Impact Testing
The use of Dart Impact Tester is prevalent in a wide range of sectors, including:
- Plastic film manufacturing: Ensuring uniform thickness and strength
- Food and beverage packaging: Avoiding spoilage due to ruptures
- Medical and pharmaceutical: Compliance with sterile packaging requirements
- Automotive and electronics: For flexible laminates and protective films
By collaborating with a seasoned dart impact tester manufacturer like Pacorr, these industries gain access to reliable tools that form the backbone of their quality assurance workflows.
Conclusion
Understanding the proper operating procedure of a Dart Impact Tester is essential for any organization that relies on flexible materials to protect or contain their products. With its commitment to engineering excellence and customer-centric design, Pacorr continues to set the benchmark for what manufacturers should expect from a dart impact tester manufacturer.
Whether you are setting up a new quality control lab or upgrading your existing equipment, following a structured and standardized testing protocol ensures you capture meaningful, actionable data every single time. It’s not just about passing a test—it’s about building a reputation for reliability, one impact at a time.
Thanks to Pacorr Testing instruments, we have all the required quality testing instruments that have helped us to ensure the best quality delivered to our clients.
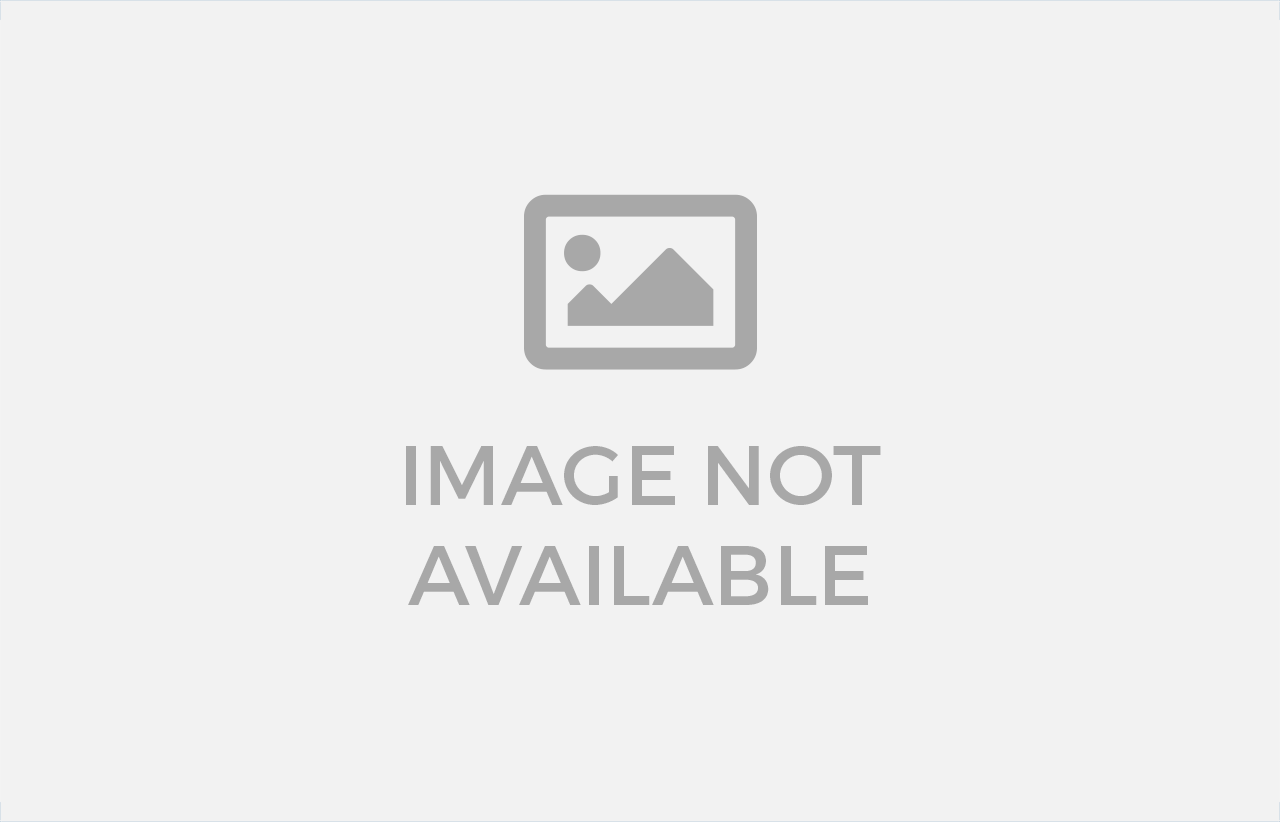
Danish
Fair Exports Pvt. Ltd.